Non-destructive testing (NDT)
Elements Of Electromagnetics
7th Edition
ISBN:9780190698614
Author:Sadiku, Matthew N. O.
Publisher:Sadiku, Matthew N. O.
ChapterMA: Math Assessment
Section: Chapter Questions
Problem 1.1MA
Related questions
Question
Non- Destructive Testing
Critical thinking essay as being professional engineer answer
2. Rank all kinds of NDT from the most expensive to the cheapest.
3. What is the most used NDT process in the industry?
Check the guide below

Transcribed Image Text:Introduction
Non-destructive testing (NDT) is a mechanism used by engineers to detect defects in materials
and structures, either during manufacturing or while in service. Typically, the methods used are
ultrasonics, radiography, magnetic particle, eddy current, dye penetrant and visual methods.
This important and growing industry is involved in applying these proven techniques and
procedures to the full range of engineering structures.
When NDT is deployed to best effect as part of the complete engineering design process, it
ensures the safe, reliable and long-lasting integrity of structures, such as power stations, aircraft,
oil & gas installations and other safety-critical plant. Every day, more than 25,000 inspections
are carried out in factories and on-site in the UK to detect defects and damage in a huge range
of products, plant and structures; it is estimated that there are more than 120,000 inspectors
operating worldwide

Transcribed Image Text:Kinds of Non-Destructive Testing
Visual and Optical Testing
Visual testing is the most widely used method of non-destructive testing (NDT). Even
the more sophisticated methods require a visual test to be performed. In other methods,
such as magnetic particle testing, after a component has been magnetised, the operator
performs a visual inspection to look for indications. Large sections of industry tend to
take visual testing for granted and pay little attention to training.
Ultrasonic Testing
Ultrasonic testing is a versatile non-destructive testing (NDT) method. Many techniques
have been developed to allow full volumetric inspection of a large range of components
made from a wide variety of materials. It is probably the most important method used in
industry, certainly in the UK.
Radiographic Testing
Radiography was one of the earliest NDT methods but, due in some way to health and
safety implications, alternative methods are replacing it, for some applications, in
industry. However, radiography remains one of the two main volumetric NDT methods.
Eddy Current Testing
Eddy current testing is a sophisticated method of non-destructive testing (NDT) in which
shallow swirling electric eddy currents are introduced into a component, allowing the
detection of surface and slightly sub-surface discontinuities.
Magnetic Particle Testing
Magnetic particle testing is a relatively simple non-destructive testing (NDT) technique
that can be used in the detection of surface and slight sub-surface discontinuities in
magnetic materials.
Penetrant Testing
Penetrant testing is a simple non-destructive testing (NDT) method used to locate
surface-breaking discontinuities in metals and many non-metals using a penetrating
liquid.
Thermal and Infrared Testing
Thermal and infrared testing is a relative newcomer to the world of non-destructive
testing (NDT). It involves monitoring the temperature variations of objects in the infrared
portion of the electromagnetic spectrum.
Expert Solution

This question has been solved!
Explore an expertly crafted, step-by-step solution for a thorough understanding of key concepts.
Step by step
Solved in 2 steps

Knowledge Booster
Learn more about
Need a deep-dive on the concept behind this application? Look no further. Learn more about this topic, mechanical-engineering and related others by exploring similar questions and additional content below.Recommended textbooks for you
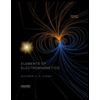
Elements Of Electromagnetics
Mechanical Engineering
ISBN:
9780190698614
Author:
Sadiku, Matthew N. O.
Publisher:
Oxford University Press
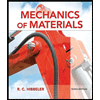
Mechanics of Materials (10th Edition)
Mechanical Engineering
ISBN:
9780134319650
Author:
Russell C. Hibbeler
Publisher:
PEARSON
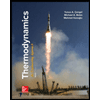
Thermodynamics: An Engineering Approach
Mechanical Engineering
ISBN:
9781259822674
Author:
Yunus A. Cengel Dr., Michael A. Boles
Publisher:
McGraw-Hill Education
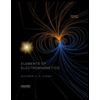
Elements Of Electromagnetics
Mechanical Engineering
ISBN:
9780190698614
Author:
Sadiku, Matthew N. O.
Publisher:
Oxford University Press
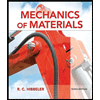
Mechanics of Materials (10th Edition)
Mechanical Engineering
ISBN:
9780134319650
Author:
Russell C. Hibbeler
Publisher:
PEARSON
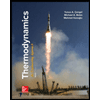
Thermodynamics: An Engineering Approach
Mechanical Engineering
ISBN:
9781259822674
Author:
Yunus A. Cengel Dr., Michael A. Boles
Publisher:
McGraw-Hill Education
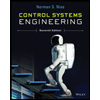
Control Systems Engineering
Mechanical Engineering
ISBN:
9781118170519
Author:
Norman S. Nise
Publisher:
WILEY
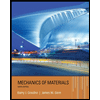
Mechanics of Materials (MindTap Course List)
Mechanical Engineering
ISBN:
9781337093347
Author:
Barry J. Goodno, James M. Gere
Publisher:
Cengage Learning
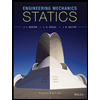
Engineering Mechanics: Statics
Mechanical Engineering
ISBN:
9781118807330
Author:
James L. Meriam, L. G. Kraige, J. N. Bolton
Publisher:
WILEY